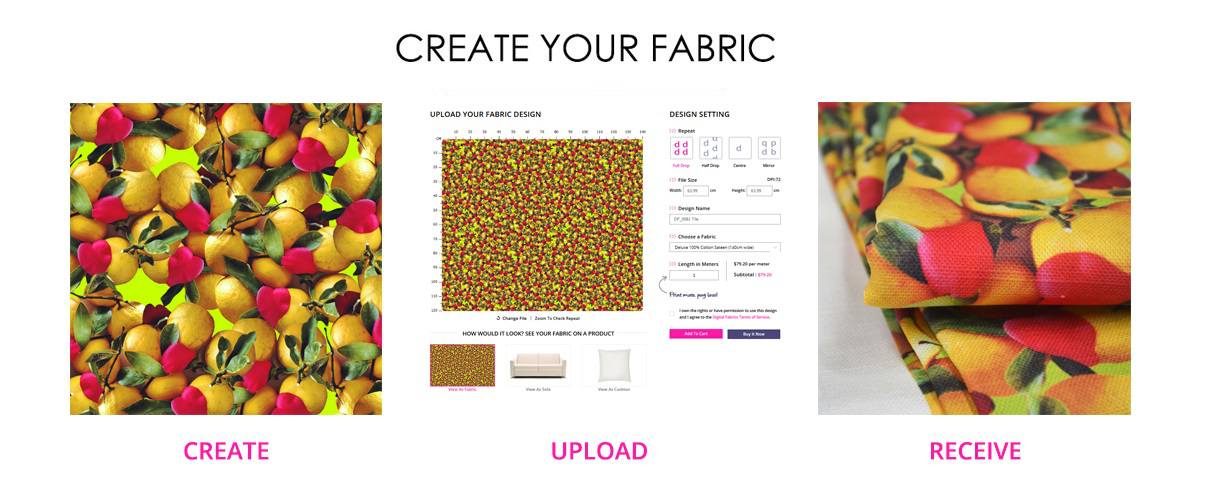
In the old world, customers had to work on specs and order sheets, carefully making sure that all information passed to the print house were correct and the files print-ready. Approving the order, approving the print proof and only then proceeding to print production with fingers crossed there were no mistakes.These may seem to be just small steps, but in reality are a huge burden on efficiency – everything is manual and takes longer than it should. We have removed meaningless and time consuming paperwork and offer our clients the ability to upload their files online, instantly check their work and order.
Digital Fabrics Fabric Uploader was specially developed to simplify and streamline the ordering process for our customers, it is the quickest and most cost-effective way to turn designs into fabric!
So toss your paperwork, just upload your design and we will take care of the rest.
Watch how its done!
Would you like to print your own fabric? Start here!
Today we are doing a happy dance! Our fabric uploader is here! From now on ordering your fabric is a fun and easy process. With a few clicks you can upload the design, preview the results and get your order under way. This is the quickest and most cost-effective way to turn your digital designs into fabric!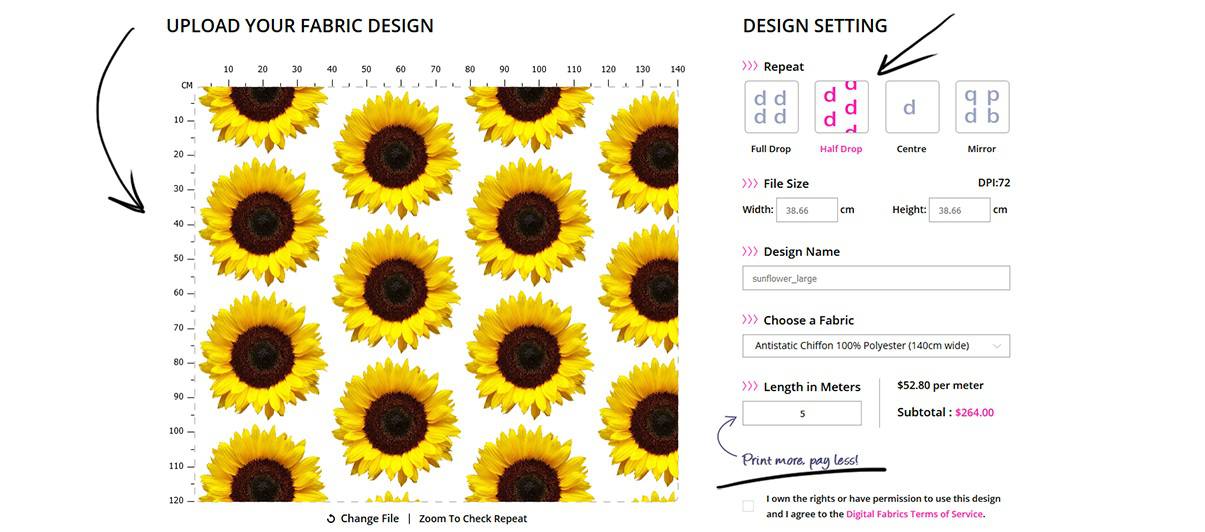
With our online FABRIC UPLOADER you can:
- Upload your design
- Choose a repeat type suitable for your design
- Check your file size and quality
- Check if your design repeats seamlessly
- See how your design will look on a product
- Order and pay in an instant of course
and with all of that NO SET UP or extra fabric cost!
Order your fabric now or just have a little play and please let us know what you think and your experience. Your feedback is always heard and appreciated!
Recently we have collaborated with Jocy from Pink Chocolate Break. She is an outstanding DIYer and very stylish creative individual. Jocy used our Tulip Time design printed on ponti fabric and created a beautiful Spring Jacket.
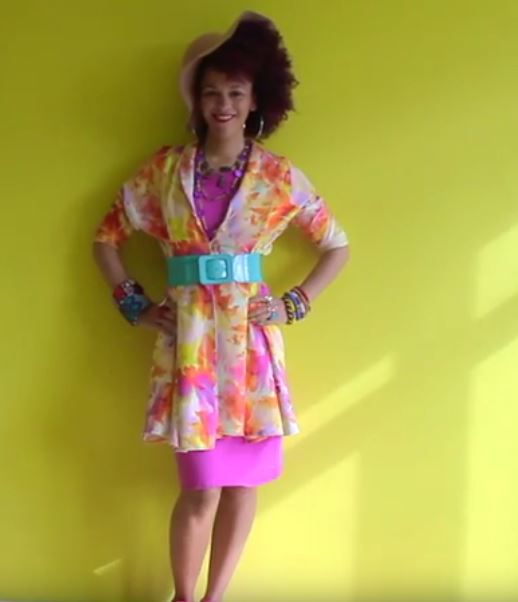
She is courageous and creative, she will inspire you to create beyond any rules and fear. Watch her outstanding creative skills and her beautiful jacket!
Essentially polyester is a man-made synthetic plastic resin substance. Polyester can be produced in sheet form, for items like PET bottles, or fibre form for all kind of textiles.
Polyester fabrics are heat sensitive and can be manipulated with high heat and pressure such as giving the fabric permanent pleats, laser cut with patterns and shapes. Polyester fibres can be produced in various forms allowing the manufactured fabric to imitate characteristics of fabrics traditionally produced in natural fibres.
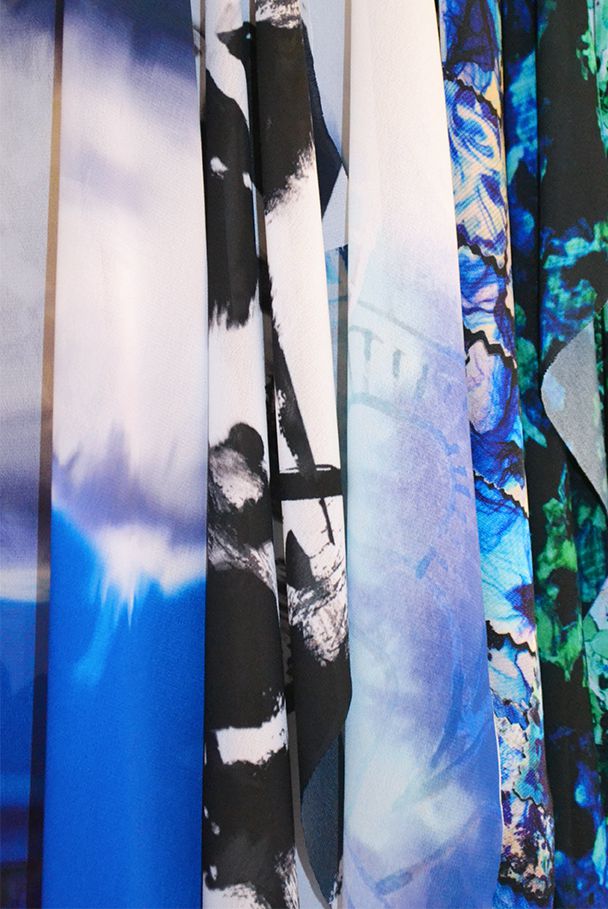
Polyester fabrics are highly stain resistant and there is only one particular type of dyes that can alter the colour or polyester fabrics, known as disperse dyes. While these dyes can be applied to the fabric in several ways, the most common way is by dye-sublimation. Dyes are printed onto a paper substrate which is then pressed into the fabric using high temperatures and pressure. The pressing process bonds the dyes to the polyester fibres of the fabric meaning that they will never fade or wear.
Polyester fibres can also be recycled, using less energy than virgin polyester and less water than organic natural fibre production, which leads to some considering recycled polyester (rPET) a sustainable fabric for future generations. The fabric printing method of dye-sublimation is a completely dry process has no water usage and while the paper is a waste by product, all dye is absorbed by the fabric leaving no dye waste.
Natural fabric is woven or knitted from fibres that occur in our natural world. All three sectors of nature; animal, vegetable and mineral produce fibres that can be used in fabric production.
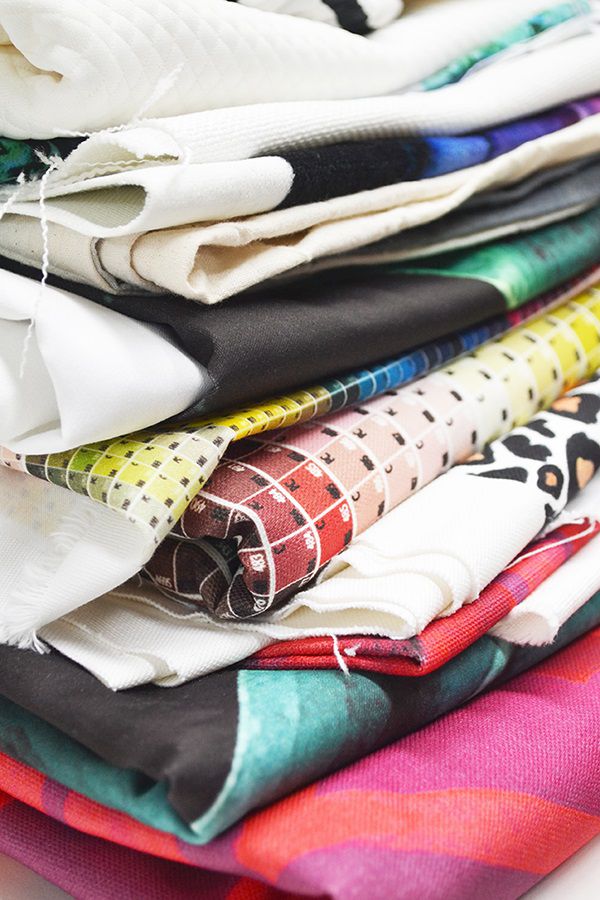
Vegetable, or more commonly classed cellulose-based fibres, include cotton, flax, jute, hemp and bamboo. Each fibre type is derived from a specific part of the plant such seed hair, stem, leaf, husk etc. and consist mainly of cellulose substance.
Animal fibres include wool and silk and consist exclusively of proteins. While wool fabric is most commonly produced from the fleece of sheep, it also includes fleece from alpacas. The hairs or fibres of other animals are also constructed into fabric including rabbit fur, angora fabric and mohair.
Silk is the other notable fibre from an animal, but unlike other animal fibres, it is not made from the hair or fur covering the animal. It is the continuous thread of the spun cocoon of moth larvae. An extensive process is required to produce one silk fibre and in turn, produce silk fabric maintaining its exclusive divine nature.
Mineral fibres are less widely used in production for fashion or interior fabrics but can still be used in an industrial application. Fine drawn threads of metallic fibres can be used on regular textile machinery and are often spun or woven in combination with other fibres to make a length of fabric for industrial use.
Through dealing with a lot of creatives we came to realise that some are having difficulties on setting up their artwork digitally into a seamless repeat, so we decided to help and after research we have put together a small collection of useful tutorials in Photoshop and Illustrator. So if you are trying to wrap your head around repeating pattern, these are for you.
- A Beginner’s Guide to Digital Textile Printing (from Design.tutsplus.com)
//design.tutsplus.com/tutorials/a-beginners-guide-to-digital-textile-printing–vector-3189
- How to make a Repeat Pattern (from DesignSponge.com)
//www.designsponge.com/2008/05/welcome-julia-and-how-to-make-a-repeat-pattern.html
- Exploring Photoshop: Designing Repeat Patterns (from Creative-Cloth.com)
//www.creative-cloth.com/photoshop-elements-tutorial-designing-repeat-patterns/
- Adobe Illustrator for Fashion and Textile design: Print for flat sketch (from Fashion Chalkboard)
Part 1: https://www.youtube.com/watch?v=5HalcOTtxgo
Part 2: https://www.youtube.com/watch?v=QFV68tAi88k
- Create beautiful repeating Patterns (from DigitalArtsOnline.co.uk)
//www.digitalartsonline.co.uk/tutorials/illustration/create-beautiful-repeating-patterns/
Interested on how to make your custom cushions?
Here are some helpful steps on how to set up your artwork ready to print with us.
You can print custom cushions from any type of design photographic, hand drawn/painted, created in Photoshop or Illustrator, the possibilities are endless! Any size, any shape, front and back or just front panels of cushions.
For this how-to we chose to paint beautiful Orchids in watercolour. Once painting is finished and dry we digitized the artwork by scanning it at high dpi of 300, artwork also can be photographed.
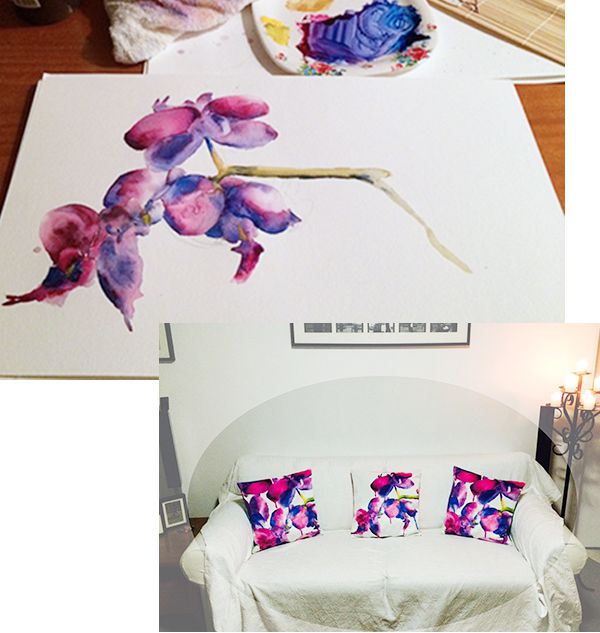
After artwork is scanned and manipulated to desired colour and placement create a new canvas in RGB colour mode, 48 x 48 cm for finished size cushion cover of 45cm x 45cm including 1.5cm seam allowance on all sides of the cushion covers.

To help remember that there is seam allowance on the artwork put guidelines on all sides 1.5cm in (these guidelines won’t show when printed). Place an artwork on art board, play around with the placement until you get the look you are after and be mindful that anything outside of the guidelines will not be seen. We print digitally onto white fabric, for this specific cushion we wanted a white background so we left the background white, if you want a colour background you can do so by creating a new layer with the colour and placing it behind the artwork.
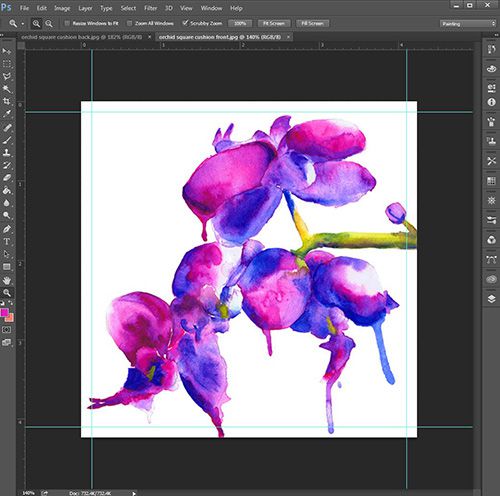
When you are happy with the results you can flatten your artwork and save, artwork can be saved as either a JPEG or TIFF.
Repeat these steps for the back of the cushion cover, if you want a certain colour for the back, drop in the colour you want into the layer.
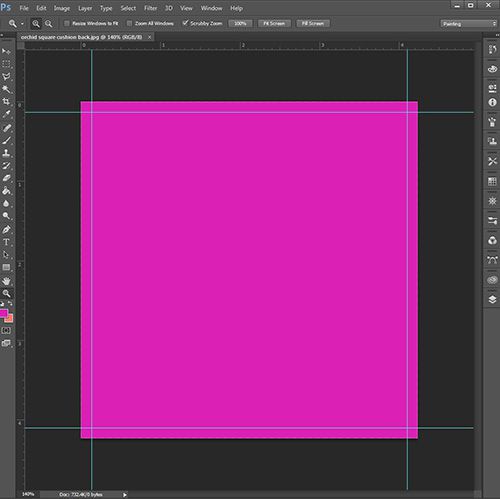
Once all is in order and your order is ready to proceed leave it to us and we can do the rest, your cushion covers will be done in no time.
We hope this helps you on your way to creating some amazing custom cushion covers to spice up your home.
Happy Designing!
The Digital Fabrics Team
Save
Save
Save
We have to admit we love DIY’s and what better than a DIY using our fabric’s. We found this tutorial on how to make your own lampshade and we are excited to try it out.
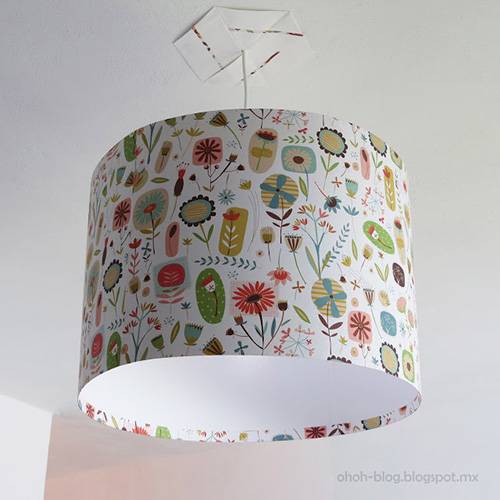
DIY lampshade Ohoh-blog.blogspot.com
Now we just have to decide which fabric to choose, here is an idea using prints from out print collection. All prints are now available to be printed on our stock fabrics, you can check out all our designs on our website.
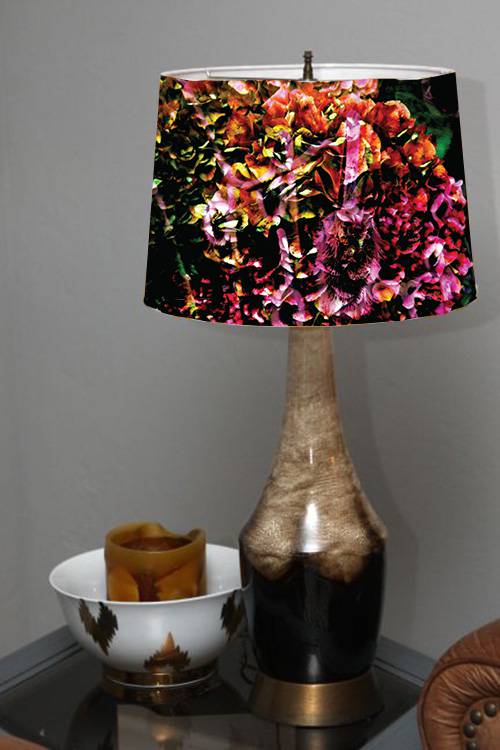
DIY lampshade idea with DF design applied
Images: Ohohblog.com and Pinterest.
We live in a very “international” age where it’s pretty impossible to live in any part of this country and not have access to information about a plethora of subjects and issues spanning the globe. And whether or not you pay much attention to it all or a little bit, at some stage you’re bound to come across sign posts for key factors that essentially impact Australians and their economy.
For example, perhaps up until this year you had paid little to no attention to where the clothes on your back were actually produced and then there was the absolutely devastating building collapse of the clothing factory in Bangladesh.
Perhaps this tragedy has highlighted some significant areas for consideration including what is the best production practice for Australian fashion houses. This brings us to print runs produced off shore, predominantly in China but increasingly in Korea and India, compared to printing on our own sunny shores. Should we be pushing for one over the other or is there a happy medium that can be forged with cooperation from members of the TCFA industry bodies and government?
Clearly price point is a huge factor and although the minimum wage for factory workers in these countries is well below what we would consider acceptable for ourselves, if we were to take away their source of income altogether by ceasing production completely, what does that do to their livelihood? And yet to support innovation and growth within Australia for both screen and digital printing is to continue to promote our own economic growth with an increased work force and encourage companies to stay local.
You can’t deny that China in particular has a rich history of fabric innovation being the first to cultivate and produce silk. Neither can you dismiss India and her surrounds for their impact on international printing trends and practices. But it would be great if right here in our own backyard we were given the opportunity to establish a stable and reliable fashion printing industry on a large scale.
The printing that is currently offered here in Australia has some key advantages and should be taken advantage of. Companies can deal directly with printers giving them a greater amount of control from initial strike off to full bulk runs. This in turn reduces time pressures by limiting the back and forth waiting for shipments or time zone constraints. Minimums are generally lower which means sampling can be produced with a lower risk and greater flexibility of having multiple print styles. And on an environmental note, the freight back and forth overseas is greatly reduced lowering emissions.
So keep up to date on all that international news, live globally, but support Australian industries, print local, print with Digital Fabrics!
We have found a few great websites that assist fashion designers with starting up their own business. The websites we found assist designers with inspiration, keeping up to date with the latest trends, and websites that help with making, grading, pattern making, marketing and much more. We thought we would share with you our favourite and most helpful websites. If you have a favourite website for emerging designers, share it with us!
Start up fashion
Information on how to start up a fashion label, supplying articles on where to find makers for our American based followers, articles on how to market your product and articles on how to sell. This website has a lot of resources for emerging designers.
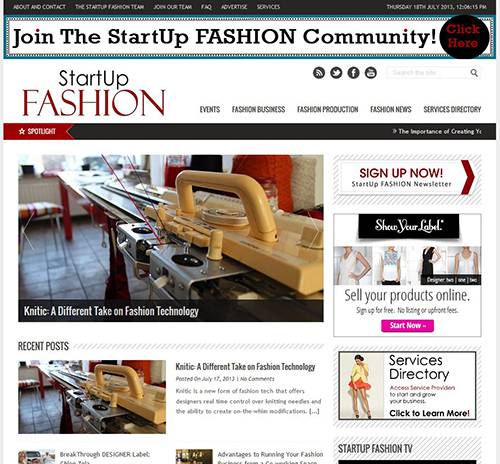
startupfashion.com
Business of Fashion
BOF featured an array of fashion articles, keep up to date with what’s happening fashion wise around the world and step by step points on how to start a fashion label and how to market.
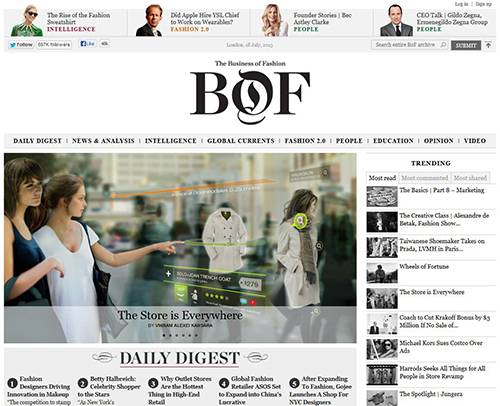
www.businessoffashion.com
Business of fashion, 8 steps to start your own fashion business
We came across this great article on the BOF website, 8 steps to start your own fashion business.
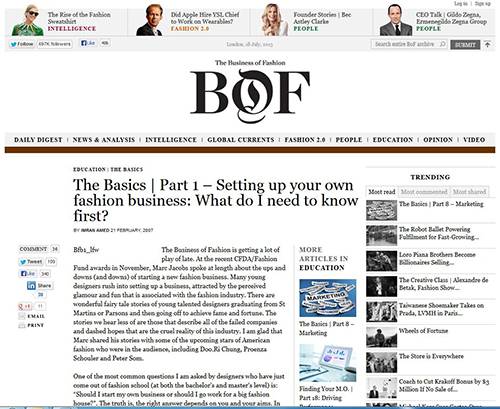
www.businessoffashion.com/2007/02/the-business-of-fashion-basics-1-setting-up-your-own-fashion-business-what-do-i-need-to-know-first.html
Ragtrader
Rag trader is a premium Australia directory for everyone in the creative industry. You’ll have to sign up to this website and pay a subscription fee, but it is well worth the money to access fashion agents, textile agents, suppliers, labels and so much more contacts.
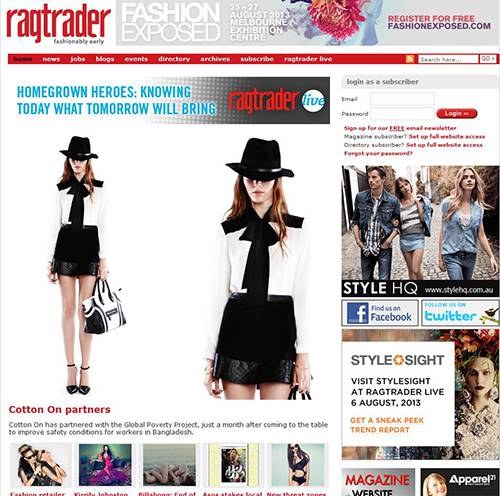
www.ragtrader.com.au/index.cfm
AusIndustry
This Australian government website is aimed at helping small textile business in Australia. The Textile, Clothing and Footwear (TCF) Small Business Program provides grants of up to $50,000 for projects to improve the business enterprise culture of established TCF small businesses that have not received grants or qualify for assistance from other TCF programs. Worth a look for all small fashion business’.
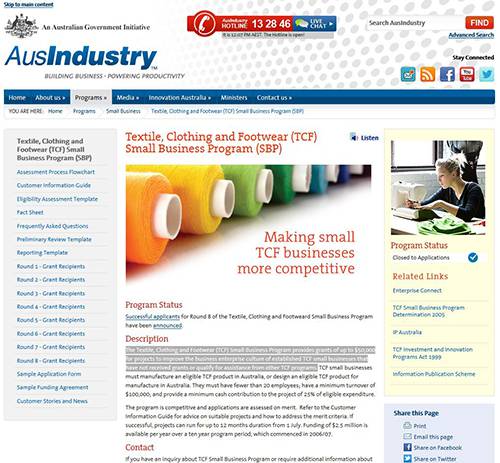
www.ausindustry.gov.au/programs/small-business/tcf-sbp/Pages/default.aspx
Fashion shop till u drop
Olena Lugassi runs one on one private design tuition and fashion online courses for designers who want to start their own business.
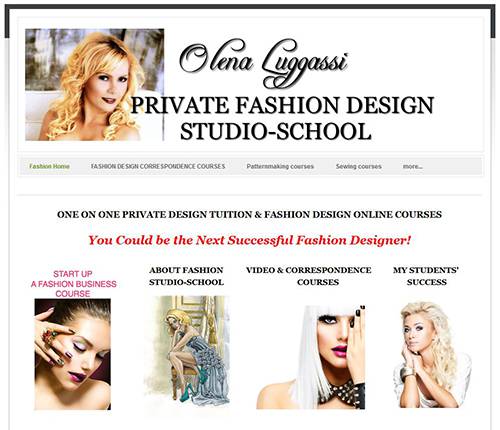
www.fashionshoptilludrop.com/index.html
Launch Initiative
Assisting designers from the start providing pattern making, grading, digitizing, sample machining, fabric advice and production services.
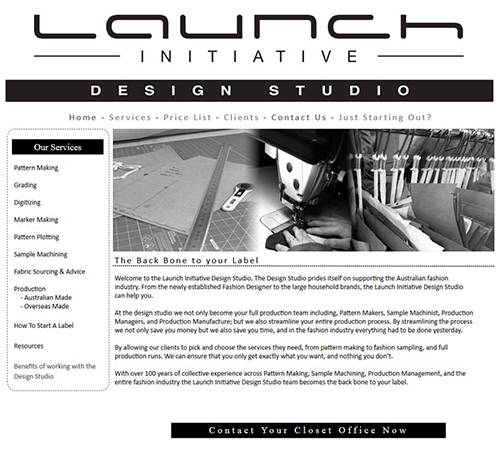
www.launchindesignstudio.com/index.html
Elizabeth Sonter
Elizabeth Sonter provides a pattern making and grading service.
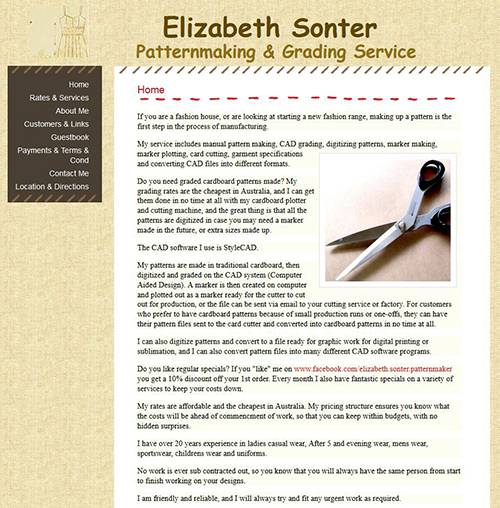
elizabethsonter.webs.com